Realidad Virtual Stellantis: Así Transforma la Producción de Autos
Descubre cómo la Realidad Virtual Stellantis optimiza la producción de autos. Conoce el VR Lab que revoluciona la fabricación automotriz y mejora la calidad. Entérate aquí.
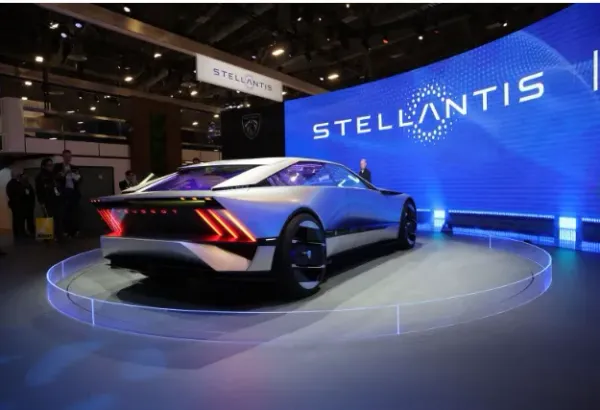
En el vertiginoso mundo de la fabricación automotriz, la búsqueda constante de eficiencia, seguridad y calidad impulsa a los grandes grupos a explorar fronteras tecnológicas. Uno de los ejemplos más fascinantes de esta evolución se encuentra en la estrategia de producción global de Stellantis, específicamente en su innovador laboratorio de realidad virtual. Ubicado discretamente pero estratégicamente en el Centro de Tecnología de Chrysler en EE.UU., el VR Lab de Stellantis no es solo un espacio con tecnología avanzada; es el núcleo de una revolución en la forma en que se conciben, diseñan y validan las líneas de ensamblaje.
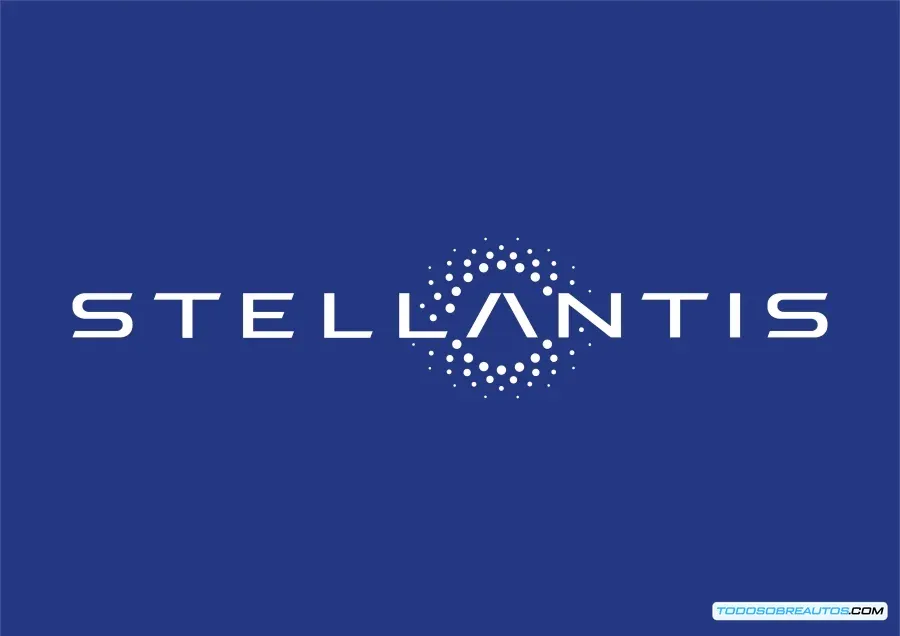
Desde su apertura en 2018 y a través de continuas actualizaciones, este laboratorio se ha convertido en una pieza fundamental para asegurar que los vehículos que llegan a las manos de los consumidores sean el resultado de procesos optimizados y libres de errores detectados tempranamente. Aquí, la *realidad virtual Stellantis optimiza producción* al permitir a los ingenieros y operarios interactuar con simulaciones digitales completas antes de que se mueva una sola pieza física en la planta.
De los Videojuegos a la Fábrica: La Tecnología Detrás del Laboratorio
Lo que hace único al VR Lab de Stellantis es su audaz adaptación de tecnologías y principios provenientes de industrias aparentemente ajenas a la manufactura pesada, como son la arquitectura, el cine y, notablemente, el desarrollo de videojuegos. Lejos de ser un simple gimmick, estas herramientas tecnológicas se aplican con rigor industrial para resolver problemas complejos en el mundo real.
El laboratorio incorpora un conjunto de tecnologías avanzadas que trabajan en conjunto: la Realidad Virtual (RV) tradicional, sistemas de captura de movimiento precisos para rastrear interacciones humanas, simulaciones de piezas basadas en la física que replican el comportamiento de componentes reales, y la integración de gemelos digitales que ofrecen visualización en tiempo real y precisión de datos. Esta fusión tecnológica permite no solo ver una representación virtual de la línea de ensamblaje, sino también interactuar con ella de forma inmersiva, manipular objetos virtuales y evaluar escenarios con una fidelidad sorprendente.
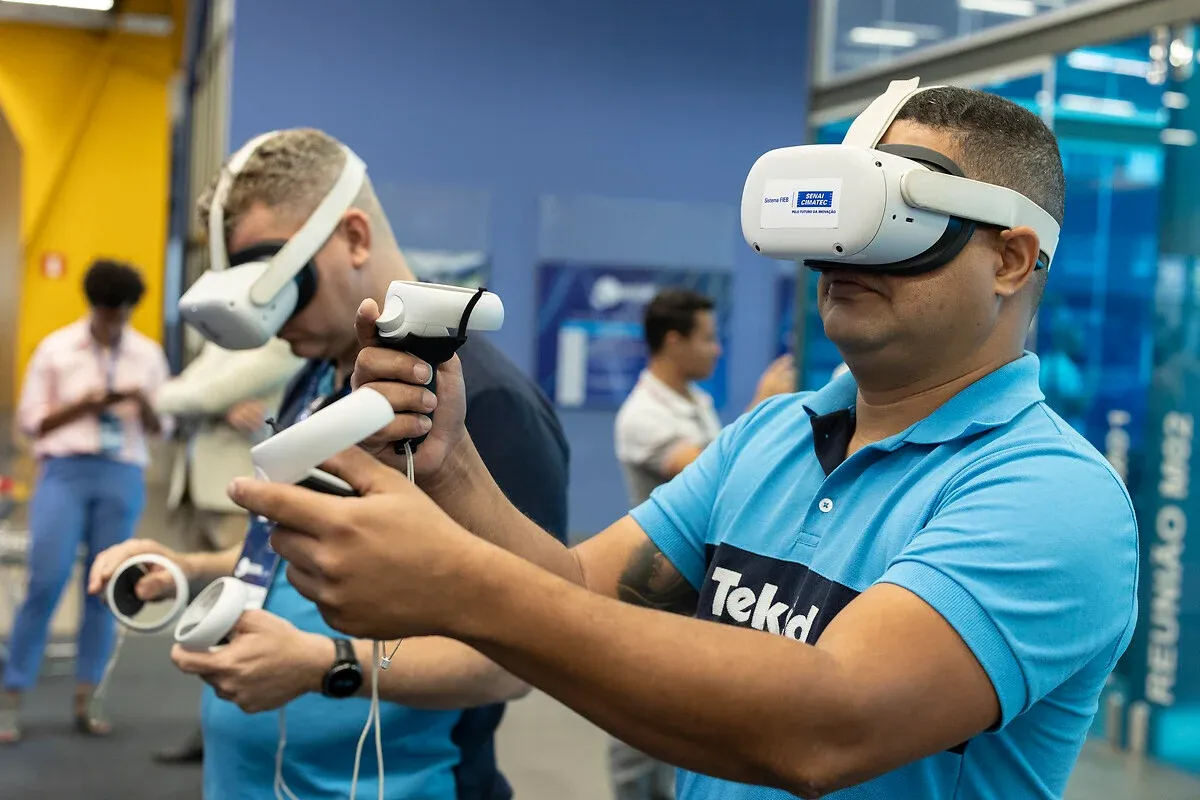
Simulación Inmersiva: Optimizando Diseño y Procesos Antes de Producir
El propósito central del VR Lab es simple pero poderoso: encontrar y resolver desafíos de diseño, herramientas y procesos *antes* de que se inicie la producción a gran escala. Tradicionalmente, muchos de estos problemas solo se descubrían durante la fase de pre-producción física o incluso en la línea de ensamblaje real, lo que generaba costosos retrasos y retrabajos.
Mediante la simulación inmersiva a gran escala que ofrece el laboratorio (con un espacio dedicado de 20 por 24 pies dentro de una instalación de 40 por 42 pies), los equipos de ingeniería pueden simular estaciones de trabajo completas y flujos de ensamblaje. Esto les permite identificar cuellos de botella, evaluar la viabilidad de una herramienta específica, probar la secuencia óptima de instalación de componentes, y detectar posibles interferencias o dificultades en el proceso de ensamblaje. Este enfoque proactivo, habilitado por la *realidad virtual Stellantis optimiza producción* significativamente al evitar problemas potenciales que, de otro modo, impactarían la eficiencia y el costo de fabricación.
Ergonomía y Seguridad: El Impacto Directo en los Trabajadores
Más allá de la pura eficiencia de la línea, uno de los beneficios más cruciales del VR Lab es su contribución directa a la seguridad y el bienestar de los operadores de la planta. La tecnología de realidad virtual es esencial para evaluar las posturas y movimientos de cientos de trabajadores que interactuarán diariamente con el proceso de ensamblaje.
Al recrear digitalmente las condiciones de montaje, los equipos de ergonomía pueden analizar cómo los operarios interactuarían con el vehículo y las herramientas en diferentes escenarios. Esto permite ajustar virtualmente alturas de plataformas de trabajo, definir "zonas doradas" de alcance óptimo para evitar esfuerzos innecesarios, y perfeccionar las técnicas para manipular piezas de forma segura y eficiente. Como afirma Tim Fallon, vicepresidente senior de fabricación de América del Norte, "Al identificar los problemas antes de que comience la producción, estamos haciendo que nuestras instalaciones sean más seguras y más capaces de ofrecer una calidad de clase mundial a nuestros clientes". La capacidad de ajustar estos parámetros ergonómicos en el entorno virtual antes de cualquier instalación física demuestra cómo la *realidad virtual Stellantis optimiza producción* desde una perspectiva humana fundamental.
Casos de Éxito: Ejemplos Concretos de Aplicación de la VR
La eficacia del VR Lab se demuestra en casos prácticos que han permitido a Stellantis resolver cientos de posibles problemas de ensamblaje antes de que impactaran la producción real. Un ejemplo destacado es su aplicación en las plantas de ensamblaje de camionetas de Sterling Heights y Warren.
Para tareas específicas como realizar conexiones eléctricas debajo de la carrocería de los camiones, determinar la altura óptima del vehículo en la línea de ensamblaje es crítico. Utilizando la realidad virtual, el equipo pudo simular múltiples alturas de línea en el entorno virtual. Esto les permitió asegurar que los operadores tendrían el alcance y el acceso adecuados para realizar estas conexiones de manera segura, eficiente y sin tensión ergonómica indebida. Realizar estas evaluaciones y ajustes en la fase de diseño virtual permitió establecer requisitos precisos de altura del transportador mucho antes de su instalación física, garantizando tanto la seguridad del trabajador como una preparación óptima para el inicio de la producción. Este es un ejemplo palpable de cómo la *simulación virtual Stellantis* se traduce en beneficios tangibles en el piso de la fábrica.
Integración Tecnológica: VR y Fabricación Aditiva (Impresión 3D)
La visión de innovación del laboratorio no se limita a la realidad virtual. El VR Lab también integra capacidades de fabricación aditiva, específicamente la impresión 3D. Esta tecnología complementa a la perfección las simulaciones virtuales al permitir la creación rápida de prototipos físicos de componentes o herramientas.
Si una simulación virtual sugiere una posible mejora en el diseño de una pieza o la necesidad de una herramienta especializada, la impresión 3D permite materializar esa idea en cuestión de horas para pruebas físicas rápidas. Esta capacidad de "prototipado rápido" acelera las iteraciones de diseño, reduce el desperdicio de material asociado con los métodos de prototipado tradicionales y mejora la eficiencia general del proceso de desarrollo de producción. La combinación de *realidad virtual* para simulación y visualización con impresión 3D para prototipado físico crea un ecosistema de innovación altamente eficiente.
Tabla: Tecnologías Clave y Beneficios del VR Lab de Stellantis
Para comprender mejor el alcance de este laboratorio, presentamos un resumen de sus componentes tecnológicos y los beneficios directos que aportan a la fabricación automotriz de Stellantis:
Tecnología / Característica | Beneficio Clave para la Producción en Stellantis |
---|---|
Realidad Virtual (RV) | Permite la inmersión en simulaciones a escala real de la línea de ensamblaje. |
Captura de Movimiento | Rastrea y analiza con precisión los movimientos y posturas de los operadores en el entorno virtual. |
Simulaciones Basadas en Física | Replica el comportamiento realista de componentes y herramientas virtuales. |
Integración de Gemelos Digitales | Proporciona visualización en tiempo real, precisión de datos y resolución de problemas inmersiva. |
Análisis Ergonómico Virtual | Permite optimizar alturas de estaciones, zonas de alcance y técnicas de manejo de piezas para mayor seguridad y menor tensión. |
Fabricación Aditiva (Impresión 3D) | Facilita el prototipado rápido de componentes y herramientas para pruebas físicas ágiles. |
La Visión Global: Expansión y Futuro de la Producción Inteligente en Stellantis
El éxito y los aprendizajes obtenidos en el VR Lab de Stellantis en América del Norte están sentando las bases para una iniciativa de fabricación global. Stellantis tiene planes de expandir su tecnología de realidad virtual y metodologías asociadas a través de todas sus regiones operativas. Esta expansión estratégica busca replicar los beneficios obtenidos: mejorar la calidad en la fuente, reducir el tiempo de inactividad de las líneas de producción y respaldar la visión a largo plazo de la empresa de una producción más inteligente, conectada y sostenible.
La inversión continua en tecnologías como la realidad virtual y la fabricación aditiva subraya el compromiso de Stellantis no solo con la innovación en los vehículos que fabrica, sino también en cómo los fabrica. Es un vistazo al futuro de la manufactura automotriz, donde la línea entre el mundo digital y el físico se desdibuja para crear procesos más eficientes, seguros y adaptables a las complejidades de los automóviles modernos, incluyendo la producción de vehículos eléctricos y otras tecnologías avanzadas. En este panorama, la *realidad virtual Stellantis optimiza producción* no solo para los vehículos de hoy, sino preparando el camino para los desafíos de manufactura del mañana.
Veredicto Final: ¿Hacia Dónde va la Producción Automotriz con Stellantis?
El VR Lab de Stellantis es un ejemplo destacado de cómo la industria automotriz está aprovechando tecnologías de vanguardia para redefinir sus procesos de producción. Al integrar la realidad virtual, la captura de movimiento, los gemelos digitales y la impresión 3D, Stellantis no solo está optimizando sus operaciones en términos de eficiencia y reducción de costos, sino que también está priorizando la seguridad y el bienestar de sus trabajadores.
La capacidad de detectar y resolver cientos de problemas potenciales en la línea de ensamblaje en una fase temprana del ciclo de diseño es un cambio de paradigma que ahorra tiempo, dinero y previene problemas de calidad en los vehículos finales. La aplicación práctica en la optimización de tareas ergonómicas en plantas de camionetas es una prueba clara de su valor. La visión de expandir esta tecnología globalmente sugiere que Stellantis ve la *realidad virtual* no como un experimento aislado, sino como un pilar fundamental para su futuro en la manufactura. En definitiva, la inversión en *realidad virtual Stellantis optimiza producción* de una manera integral, sentando un precedente interesante para el resto de la industria.
¿Preguntas o Comentarios? ¡Te Leemos!
¿Qué te parece el uso de la realidad virtual en la fabricación de automóviles? ¿Creías que estas tecnologías tenían un impacto tan directo en la seguridad y eficiencia de las plantas? ¿Sabes si otros fabricantes están empleando enfoques similares? ¡Déjanos tus opiniones, dudas o cualquier otra reflexión en la sección de comentarios abajo!
Preguntas Frecuentes
¿Qué es exactamente el VR Lab de Stellantis y dónde se encuentra?
El VR Lab (Laboratorio de Realidad Virtual) de Stellantis es un centro de innovación tecnológica dedicado a optimizar los procesos de producción automotriz. Está ubicado en el Centro de Tecnología de Chrysler en Estados Unidos. En este espacio, se utilizan tecnologías de realidad virtual y simulación para diseñar, validar y mejorar las líneas de ensamblaje antes de que se implementen físicamente en las plantas de producción. Su objetivo principal es detectar y resolver problemas potenciales en las fases iniciales, lo que conlleva mejoras significativas en eficiencia, seguridad y calidad.
¿Cómo ayuda la realidad virtual a mejorar la ergonomía en las plantas de Stellantis?
La realidad virtual permite simular digitalmente las estaciones de trabajo y los movimientos de los operarios en la línea de ensamblaje. Esto facilita la evaluación de posturas, alcances y técnicas de manipulación de piezas. Los especialistas en ergonomía pueden identificar posibles riesgos de lesiones o fatiga y realizar ajustes virtuales, como modificar la altura de las plataformas o redefinir las zonas de alcance óptimo. Al implementar estos cambios antes de la producción real, se minimiza el esfuerzo físico innecesario, se mejora la seguridad y se promueve el bienestar de los trabajadores.
¿Qué tipo de tecnologías se integran en el VR Lab, aparte de la realidad virtual?
Además de la realidad virtual, el VR Lab integra diversas tecnologías avanzadas. Entre ellas se encuentran los sistemas de captura de movimiento para rastrear con precisión las interacciones humanas, las simulaciones basadas en la física que replican el comportamiento de los componentes reales y la integración de gemelos digitales, que ofrecen visualización en tiempo real y datos precisos. También se utiliza la fabricación aditiva, o impresión 3D, para crear prototipos rápidos de componentes o herramientas, lo que acelera el proceso de diseño y mejora la eficiencia general.
¿Cuál es el impacto de la realidad virtual en la reducción de costos de producción?
La realidad virtual permite identificar y resolver problemas de diseño y procesos antes de que se inicie la producción a gran escala. Tradicionalmente, muchos de estos problemas se detectaban durante la fase de pre-producción física o incluso en la línea de ensamblaje, lo que generaba costosos retrasos y retrabajos. Al simular estaciones de trabajo y flujos de ensamblaje en un entorno virtual, los equipos de ingeniería pueden evitar cuellos de botella, evaluar la viabilidad de herramientas y optimizar la secuencia de instalación de componentes, lo que reduce significativamente los costos asociados con errores y modificaciones posteriores.
¿Cómo se relaciona la realidad virtual con la visión de Stellantis sobre la producción inteligente y sostenible?
La inversión en realidad virtual es una pieza clave en la estrategia de Stellantis para lograr una producción más inteligente, conectada y sostenible. La realidad virtual permite optimizar los procesos de fabricación, reducir el desperdicio de materiales y mejorar la eficiencia energética. Además, al priorizar la seguridad y el bienestar de los trabajadores, la realidad virtual contribuye a un entorno de trabajo más sostenible y responsable. La expansión de esta tecnología a nivel global demuestra el compromiso de Stellantis con la innovación y la mejora continua en sus procesos de producción.
¿Qué beneficios concretos ha traído la aplicación de la realidad virtual en las plantas de ensamblaje de camionetas de Stellantis?
Un ejemplo claro es la optimización de las conexiones eléctricas debajo de la carrocería de los camiones. Utilizando la realidad virtual, el equipo pudo simular diferentes alturas de la línea de ensamblaje y determinar la altura óptima para que los operarios realizaran estas conexiones de manera segura, eficiente y sin tensión ergonómica. Esta evaluación virtual permitió establecer requisitos precisos de altura del transportador antes de su instalación física, lo que garantizó tanto la seguridad del trabajador como la preparación para la producción. Este tipo de mejoras se traducen en una mayor eficiencia, menor riesgo de lesiones y una mejor calidad en el producto final.